Wasserstrahlschneiden
Trennen fast aller Materialien in bester Qualität
max. Werkstückgröße 3000 x 1500 x 130 mm
max. Werkstoffdicke 130 mm (werkstoffabhängig)
max. Werkstückgewicht 1250 kg
Schnittqualität in 5 Stufen
automatischer Winkelausgleichs-Schneidkopf für nahezu konusfreien Schnitt
Herstellungstoleranzen von ± 0,1mm
Positioniergenauigkeit ± 0,025 mm
kleinstmögl. Innenradius 0,4 mm
Wasserstrahlschneiden
bei Dick & Dick
Bereits seit dem Jahr 1996 setzen wir das Wasserstrahlschneiden für die Fertigung und Bearbeitung unserer Kundenbauteile ein. Insbesondere bei hohe Materialdicken und wärmeempfindlichem Material empfehlen wir Ihnen dieses Trennverfahren mittels Hochdruck-Wasserstrahl.
Stets haben wir eine Reihe der gefragtesten Materialien wie Edelstahl, Stahl und Aluminium auf Lager, um unsere Lieferzeit so kurz wie möglich zu halten.
Ihr Projekt direkt online anfragen
Schnelle Anfragen
Angebote direkt per Email oder Online-Formular
Vielfalt
Sehr große Materialauswahl
Veredelung
Umfangreiche Nachbehandlung
Offene Fragen
Beratung und Hilfestellung
Lieferzeit
Schnelle Produktion anhand Ihrer CAD-Daten
Kosten
Faire Fertigungspreise
Technischer Hintergrund
Das Wasserstrahlschneiden arbeitet nach einem recht einfachen Prinzip: Ein feiner Wasserstrahl wird durch starken Druck auf sehr hohe Geschwindigkeit beschleunigt und trifft auf die Oberfläche des Werkstücks. Der Hochdruckwasserstrahl verursacht durch den Materialabtrag das Trennen des Materials.
Je nach zu bearbeitetem Material kann dem Wasser ein Abrasivmittel zugesetzt werden, um die Schneidwirkung zu steigern.
Der spannungsfreie Schneidprozess erzeugt keinen Wärmeeintrag in das Material und kann daher für das Trennen von nahezu allen Materialien verwendet werden
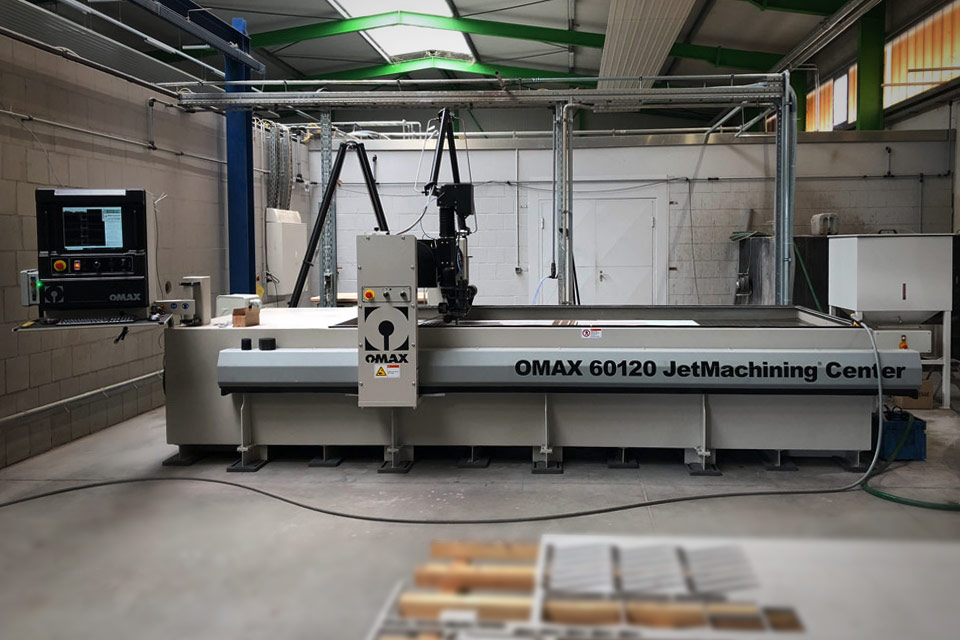
Vorteile
Wasserstrahlschneiden
- Werkstoffschonendes Schneiden ohne Wärmeentwicklung
- keine Werkstoffverhärtungen, Verfärbungen oder gar Risse
- optimale Werkstoffausnutzung durch CAD-Schachtelpläne
- keine Werkzeugkosten wie beim Fräsen oder Stanzen
- geringere Rüstzeiten und kürzeste Lieferzeiten, ideal für Einzelteilfertigung und Prototypenbau
- nahezu jeder Werkstoff ist schneidbar
- umweltfreundlich
Nachteile
Wasserstrahlschneiden
- je nach Schnittqualität geringe Schnittgeschwindigkeit
- Wasserkontakt mit dem Material
- Wasseraufbereitung notwendig
Schnittqualitäten
Wir sind in der Lage, beim Wasserstrahlschneiden verschiedene Schnittqualitäten umzusetzen, je nach den von Ihnen gestellten Anforderungen an ihr Produkt.
Damit erhalten Sie die zu Ihrem Produkt passende jeweils günstigste und schnellste Bearbeitung.
Trennschnitt
Ermöglicht das schnellste und günstigste Trennen von Material. Die Schnittränder am Material sind rau.
Insbesondere im unteren Bereich tritt eine Riefenbildung (Schlepp) auf. An der Austrittsstelle befindet sich ein starker Grad.
Wir empfehlen dieses Verfahren, wenn die Teile für eine intensive Nachbearbeitung vorgesehen sind.
Grobschnitt
Der Grobschnitt ist sehr ähnlich dem Trennschnitt. Aufgrund der geringeren Schneidgeschwindigkeit bietet dieser aber etwas weniger Riefenbildung
Normalschnitt
Der Normalschnitt liefert eine gute Balance zwischen Geschwindigkeit und Qualität des Schnittes und ist für die meisten Anwendungen ausreichend.
Qualitätschnitt
Die Schnittflächen (beidseitig) sind glatt und weisen kaum Unebenheiten durch eine Riefenbildung auf. Der Grad an der Austrittsstelle ist gering.
Eine Nachbearbeitung des Materials ist daher meist nicht notwendig.
Feinschnitt
Materialien für das Wasserstrahlschneiden
Im Gegensatz zum Laserstrahlschneiden, CNC-Fräsen oder Aluminiumsägen lassen sich mit Wasserstrahlschneiden eine Vielzahl an Materialien bearbeiten. Grundsätzlich kommt jedes nicht-wasserlösliche Material in Frage.
Metalle
Insbesondere bei sehr hohen Materialstärken empfiehlt sich das Trennen des Metalls mit Hilfe der Wasserstrahltechnik.
Einige Metalle oder Anwendungen machen ein materialschonendes Trennen notwendig. In diesen Fällen ist der Schnitt mittels Wasser ebenfalls die beste Lösung.
Kunststoffe & Gummi
Das Wasserstrahlschneiden ist ideal für das Trennen von nichtmetallischen Materialien wie zum Beispiel Kunststoffe, Elastomeren, Gummi und Dichtungsmaterialien. Da während des Schneidvorgangs keine Hitze ins Material gebracht wird, kann sich dieses nicht verziehen oder verbrennen.
Verbundwerkstoffe
In vielen Industriezweigen kommen immer häufiger Verbundwerkstoffe zum Einsatz. Diese verursachen bei anderen Trennverfahren oft sehr hohen Werkzeugverschleiß. Diese zusätzlichen Kosten können durch den Einsatz des Wasserstrahlschneidens verhindert werden.
Somit lassen sich komplexe Bauteile aus Carbon (Kohlenstofffaser), Glasfaser, Kevlar und Ähnlichem kosteneffektiv umsetzen.
Stein, Keramik & Fliesen
Beim Schneiden von sehr harten Materialien wird dem Wasserstrahl ein Abrasiv zugesetzt.
Dadurch können wir den Schnitt von z. B. Marmor, Granit, Keramik, Naturstein, Beton und Fliesen und ähnlichen Werkstoffen umsetzen.
Glas
Das Wasserstrahlschneiden ist für das Schneiden oder Durchbohren von Glas geeignet. Aufgrund der geringen Schnittfugenbreite können auch komplizierte Muster mit hoher Qualität der Schnittkanten ermöglicht werden. Zum Teil kann es beim Anstich des Materials zu Bruch kommen.
Schnittkanten werden milchig und undurchsichtig. Wir empfehlen Testzuschnitte.
Holz- & Papierprodukte
Der Zuschnitt von Holz- und Papierprodukten ist mit Einschränkungen möglich. Eine Wasseraufnahme des Materials lässt sich nicht komplett vermeiden.
Um die Eignung Ihres Materials zum Schneiden mittels Wasser zu prüfen, machen wir gern für Sie einige Testschnitte.
Ihr Material ist nicht dabei?
Kontaktieren Sie uns:
Veredelung & Finish
Bauteile und Modelle, welche im Wasserstrahlschnitt gefertigt wurden, können auf sehr verschiedene Weisen nachbehandelt und aufgewertet werden.
Oberflächenbehandlung
Glasperlstrahlen
Das Bestrahlen der Bauteiloberflächen mit Glasperlen erzeugt eine sehr homogene Oberflächenstruktur und dekorative Oberflächen. Durch das Bestrahlen wird zudem eine schonende Reinigungswirkung erzielt.
Die Methode kann zum Mattieren und Finishen der Metalloberflächen verwendet werden um eine hochwertige Anmutung zu erreichen. Es lassen sich dadurch sichtbare Bearbeitungsspuren an den Bauteilen nacharbeiten.
Gleitschleifen
Unsere Gleitschleifanlage ermöglicht einen schonenden Materialabtrag, insbesondere an den Kanten der zu bearbeitenden Werkstücke.
Die Werkstücke werden bei diesem Nachbearbeitungsverfahren, zusammen mit Schleifkörpern und einer wässrigen Lösung, durch oszillierende Bewegungen bearbeitet.
Schleifen / Kantenverrundung
Wir können Ihre Werkstücke mittels Schleifvlies oder Schleifscheiben sowohl entgraten als auch Kantenverrundungen vornehmen.
Mittels eines rotierenden Discwerkzeugs werden die Kanten und Oberflächen aus allen Richtungen sauber bearbeitet. Dabei wird ein feines, diffuses bzw. undefiniertes Schliffbild erzeugt.
Mittels Schleifwalzen ist auch ein paralleles Bürsten mit einer definierten Richtung möglich.
Mechanische Bearbeitung
Biegen & Abkanten
Wir können auf unseren 125 und 250 Tonnen Gesenkbiegepressen das Abkanten bis 3000mm Länge ausführen. Für die effiziente Herstellung von Kleinteilen nutzen wir eine Maschine mit einem maximalen Arbeitsbereich von 500mm.
Hochwertige Einzel- und Serienkantungen mit gleichbleibender Qualität sind durch schnelle Taktzeiten problemlos umsetzbar.
Bohren, Senken & Passungen
Einzelne Bohrungen und Bohrbilder können mittels unseres Bearbeitungszentrums nach dem Zuschnitt eingebracht werden.
Zusätzlich zur CNC Bearbeitung können Bohrungen und Senkungen auch an Handbohrplätzen vorgenommen werden. Eng tolerierte Passungen lassen sich durch das Nachreiben der Bohrungen realisieren
Gewinde schneiden
Das Einbringen von Gewinden in Ihr Werkstück ist für DIN Gewinde ab M2,5 bis M30 möglich.
Wir bieten Ihnen ebenfalls gern das Einbringen von zölligen Gewinden an.
Gewindeeinsätze & Gewindebolzen
Wir können Ihre Bauteile und Werkstücke durch das Einbringen von Gewinde- oder Helicoil-Einsätzen mit hochbelastbaren und dauerhaften Gewindelösungen versehen.
Stark belastbare Gewinde lassen sich durch das Einpressen von Gewindebolzen und Stiften auch für dünne Blechteile umsetzen.
Seit über 25 Jahren trennen wir mittels Wasser
Wir verstehen uns als Dienstleister und unser Bestreben sind vor allem unsere zufriedenen Kunden. Unser Ziel ist es, mit unseren Kunden eine langfristige Beziehung aufzubauen und gemeinsam an unseren Projekten zu wachsen.

Ihr Projekt besprechen:
(036025) – 16 30 – 0
Umwelt
Die Umweltbelastung durch das Wasserstrahlschneiden ist relativ gering, da weder Rauch oder Dämpfe entstehen und die Folgekosten beim Trennen mittels Wasserstrahl gering ausfallen. Dies liegt vor allem daran, dass keine Gefügeveränderungen wie zum Beispiel Verhärtungen an den Schnittkanten auftreten und die Schnittflächen sehr sauber gearbeitet werden können.
Für das Schneiden mittels Wasserstrahl ist kein Werkzeug notwendig. Daher können keine Verschleißerscheinungen auftreten, was die Kosten gering und gut planbar hält.
Durch das dichte Verschachteln der Einzelteile ergibt sich eine hohe Materialausnutzung, wir sind bestrebt, die Ressourcen optimal zu nutzen und Materialabfälle gering zu halten.
Metallische Reststücke werden von uns sortenrein eingelagert und dem Recycling übergeben.
Informationen zur Geschichte
Bereits im frühen 20. Jahrhundert wurde das Wasserstrahlen zum Abtragen von Material in der Bergbauindustrie eingesetzt, dies geschah damals aber mit Drücken von lediglich ca. 100 bar.
Erst in den 70er-Jahren fand das Trennen mittels Wasserstrahl Beachtung durch die Flugzeugindustrie, vorrangig durch die Firma Boeing, die das Verfahren für das Schneiden der zu der Zeit vermehrt eingesetzten Verbundwerkstoffe einsetzte.
1974 entwickelte das Unternehmen FLOW International Inc. das Abrasiv-Wasserstrahlschneiden, indem dem Wasserstrahl harte Partikel zugeführt wurden, wodurch sich die Schneidwirkung des Strahls enorm verstärkte. Dadurch erhöhte sich die Wirtschaftlichkeit und die Qualität des Verfahrens. Ab diesem Zeitpunkt stand dem Durchbruch des Trennverfahrens in der industriellen Anwendung nichts mehr im Wege.